The airframe is quite literally the backbone of any aircraft, and in the RV-3B, its lightweight yet robust design plays a critical role in performance and safety. This guide shares my detailed process for constructing the RV-3B airframe—from the first cleco to the final assembly—packed with tips and lessons learned along the way. Whether you’re an experienced builder or tackling your first kitplane, understanding each phase of airframe construction is essential for a successful build and safe operation.
Breaking Down the Airframe: Major Components
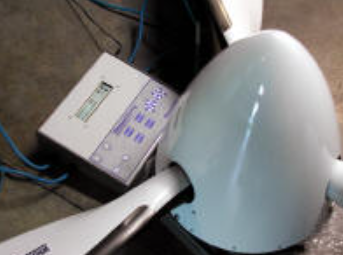
The RV-3B airframe consists of three primary sections: Wings Fuselage Empennage (tail assembly) Each of these areas brings its own set of challenges and intricacies, which I’ll break down in this guide.
Wing Construction Process
Spar Preparation
The spar is the wing’s main structural component. I began by deburring and priming the spars before assembly, ensuring every rivet hole was clean to prevent cracking over time.
Rib Assembly
Careful alignment was crucial here. I used multiple clecos to hold ribs in place before riveting, double-checking measurements at every step to maintain symmetry.
Fuel Tank Installation
This was one of the messier parts of the project. Using ProSeal, I sealed every joint meticulously to prevent future leaks. I also performed a pressure test before closing the tanks completely.
Fuselage Construction Steps
Building the Tailcone
The tailcone took shape surprisingly quickly, but ensuring perfect alignment was vital for smooth flight control response. I frequently cross-checked the centerline and stringers.
Firewall Assembly
The firewall not only separates the cockpit from the engine but also serves as a mounting point for many systems. I riveted the stainless-steel firewall carefully, ensuring all holes were sealed to prevent engine bay fumes from entering the cockpit.
Landing Gear Fittings
One challenge I faced was aligning the main landing gear mounts. Even slight misalignment can cause tracking problems on the ground, so I took extra time here.
Tail Section: Empennage Assembly
Horizontal and Vertical Stabilizers
Assembling the stabilizers required precision drilling and riveting, especially at the hinge points for the elevator and rudder.
Control Surface Alignment
Before closing up the empennage, I dry-fit all control surfaces to ensure smooth movement and no binding.
Key Tools and Materials I Used
Pneumatic rivet gun and squeezer Digital level for alignment checks Clecos in various sizes Aviation-grade sealants and primers Tungsten bucking bar for tight spots These tools saved countless hours and helped achieve professional-quality results.
Common Challenges and How I Solved Them
Misaligned rib holes: I stopped and re-measured rather than forcing rivets into place. Oil-canning on skins: Added temporary braces during riveting to prevent deformation. Fuel tank leaks: Patched minor leaks with additional ProSeal after a second pressure test.
Safety and Quality Assurance Tips
Always wear protective gear when priming and sealing. Double-check torque specs and rivet callouts before final assembly. Keep a detailed build log with photos—this helps with troubleshooting and certification later.
What’s Next After Airframe Completion?
With the airframe complete, the next phases include: Installing the firewall-forward components (engine, prop, exhaust) Wiring avionics and electrical systems Painting and final detailing The airframe lays the foundation, but there’s still a long and rewarding journey ahead to bring the RV-3B to life.
Explore More of My Build Journey
Check out these related sections to follow along with the full build process: 👉 RV-3B Detailed Airframe Build Log: Step-by-Step Documentation 👉 RV-8 Propeller Installation Guide: Lessons and Best Practices 👉 RV-8 Painting Guide: Achieve a Professional Finish